Série (5/5) : La recherche en mode BW (Brésil-Wallonie)
Quand on se promène sur le chemin de halage de la Sambre, les monticules de ferrailles qui bordent la rivière non loin de Charleroi ne passent pas inaperçus. Ils constituent la matière première de la société Comet Sambre, spécialisée dans le recyclage des métaux.
Cette activité historique (1987) du désormais “groupe Comet” (acronyme à l’époque de “Compagnie des métaux”) a connu de nombreux développements.
« Outre le recyclage de voitures hors d’usage, nous sommes également actifs dans le recyclage de déchets électriques et électroniques, mais aussi des ferrailles collectées à domicile, de la ferraille industrielle, et de celle qui provient des parcs à conteneurs ou encore des déchets de construction », explique Pierre-François Bareel, administrateur délégué de Comet Traitement, une des entreprises du groupe. La spécialité de sa société? C’est la valorisation des résidus de broyage.
Une nouvelle vie pour les résidus de broyage
« Le groupe a mis au point une filière complète et intégrée de recyclage”, détaille l’ingénieur. “D’une part, il y a la collecte et la dépollution des déchets. Ce sont les sites qui se situent sur un axe allant de Gand à Charleroi en passant par Bruxelles, Tournai, Mons et Châtelet ainsi que le nord de la France qui s’en chargent. »
« Ensuite, il y a la filière de broyage, implantée à Obourg et à Châtelet. Ici, on libère les différentes matières premières au moyen de diverses techniques: tambour magnétique, cisaille, découpe au chalumeau. 75% de cette “production” (un million de tonnes d’acier par an environ) file ensuite vers la sidérurgie pour connaître une nouvelle vie. »
Le reste, soit la fraction non-magnétique des broyeurs, est pris en charge par Comet Traitement. Cette société tente avec succès, et depuis 2002, à coups de divers projets de R&D initiés dès les années 1990, de récupérer tout ce qui est non-ferreux dans ces résidus.
« Avant cela, tout partait en décharge ou était récupéré sous forme d’énergie par pyrolyse », explique, Pierre-François Bareel. « Aujourd’hui, il est possible de recycler bien davantage cette fraction résiduelle avant de passer par la valorisation énergétique ».
Des innovations qui ont été rendues possibles grâce à la collaboration de chercheurs de l’Université de Liège, du Certech à Seneffe, mais aussi du Centre de Recherches Métallurgiques (CRM).
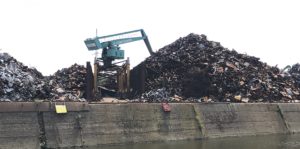
Une voiture recyclée à 96 %
« Nous récupérons désormais les métaux non-ferreux de manière industrielle, et non plus à la main, comme jadis. Cinq catégories de matières plastiques sont également valorisées. Et nous recyclons également la rouille, qui est utilisée comme un minerai de fer de substitution. »
La fraction minérale de ces résidus (sable, verre, etc.) n’est pas délaissée. « Elle peut servir de sable de substitution à celui qui est extrait de la mer du Nord pour des applications routières », dit encore l’ingénieur. « Désormais, nous récupérons par exemple jusqu’à 96 % d’une voiture hors d’usage. Bref, nous sommes passés du métier de ferrailleur à celui d’experts en recyclage. »
Ce savoir-faire wallon s’exporte désormais bien loin des berges de la Sambre. Au Brésil notamment, grâce à un coup de pouce de Wallonie-Bruxelles International et de l’Awex, l’Agence wallonne à l’exportation.
Mise au point d’une filière de recyclage à Rio de Janeiro
« Nous travaillons désormais aussi sur les transferts de technologies ou sur la mise en place d’usines utilisant à l’étranger notre expertise », reprend Pierre-François Bareel. Principalement au Japon en Amérique du Nord et en Amérique du Sud. Au Brésil, le recyclage des déchets métalliques est une préoccupation grandissante. Ce qui amène les industriels à se tourner vers des techniques de recyclage performantes.
« Dans ce cadre, nous développons un projet pilote avec le groupe brésilien Gerdau qui dispose de quatre broyeurs à métaux dans le pays. Notre collaboration concerne celui de Rio de Janeiro. C’est là que notre unité pilote se met en place. Après avoir testé la faisabilité de ce projet, nous travaillons désormais à la mise au point d’une filière de recyclage complète là-bas, en collaboration avec des scientifiques de l’université de Liège, mais aussi de l’Université de Sao Paulo », dit-il encore, avant de conclure: « nous disposons de belles technologies. Nous avons une longueur d’avance dans nos installations. L’idée est que l’on devienne là-bas un sous-traitant du groupe brésilien. »